Flow System Installation for a Northumbrian Water Treatment Works
siris2021
on
November 1, 2024
Flow System Installation for Water Treatment Works
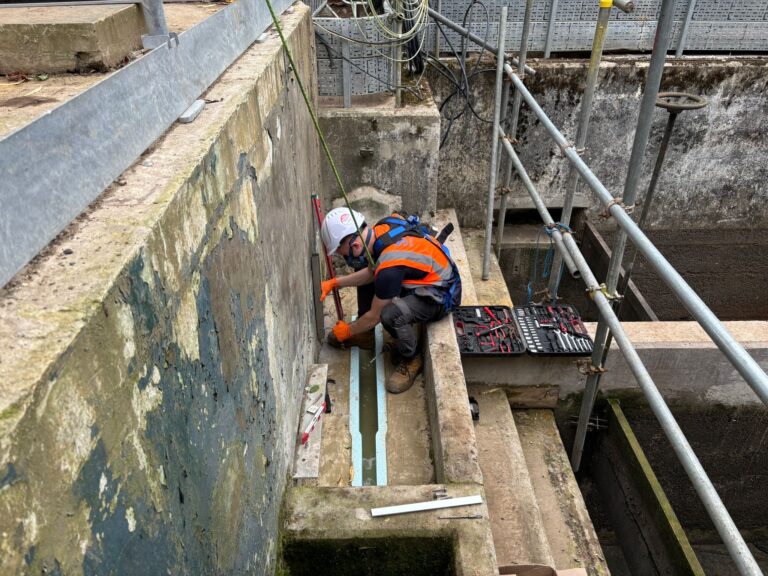
The Project
This summer, our team installed a flow system at a Water Treatment Works site.
Jamie, our Trainee Service & calibration Engineer and Jordan, our Servicing & Installation Engineer, installed a new stainless steel cross-channel bracket.
On this bracket, our team were able to mount the ultrasonic sensor over one of our 70b flume channels, so that more accurate and reliable data could be gathered from the open channel flow below.
Additionally, we fitted cable trays to the wall, allowing the sensor cable to run above ground and into a SIRIS Open Channel Ultrasonic Flow Meter, which we installed and calibrated accordingly. Now up and running, this system – with this particular application – can handle flows of up to 12.42 litres per second and is ready for its mCERTs inspection.
Why is an accurate flow system installation important?
If your site discharges – or plans to discharge – wastewater (also known as trade effluent) into the public environment, you will need a consent to discharge from your local water company, which outlines the conditions under which you are able to discharge, including your volumes of flow. Failure to adhere to these permit conditions could result in charges or even prosecution. With SIRIS Environmental, our expert team ensures your installation stays within permitted regulations for accurate monitoring and you can be confident in a system that will meet your mCERTs requirements.
The installation of an effective flow monitoring system also allows you to accurately track the amount of effluent your site discharges, which could reduce your wastewater charges and help you understand and reduce the volume you discharge into the environment.
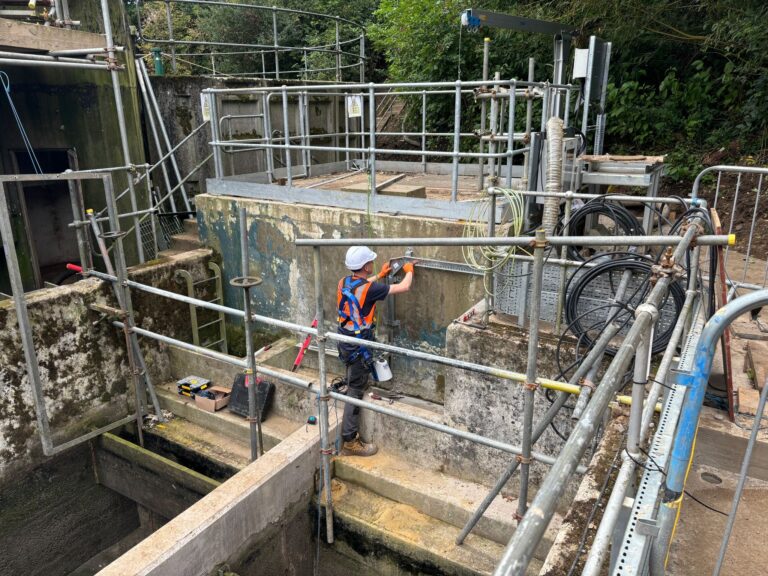
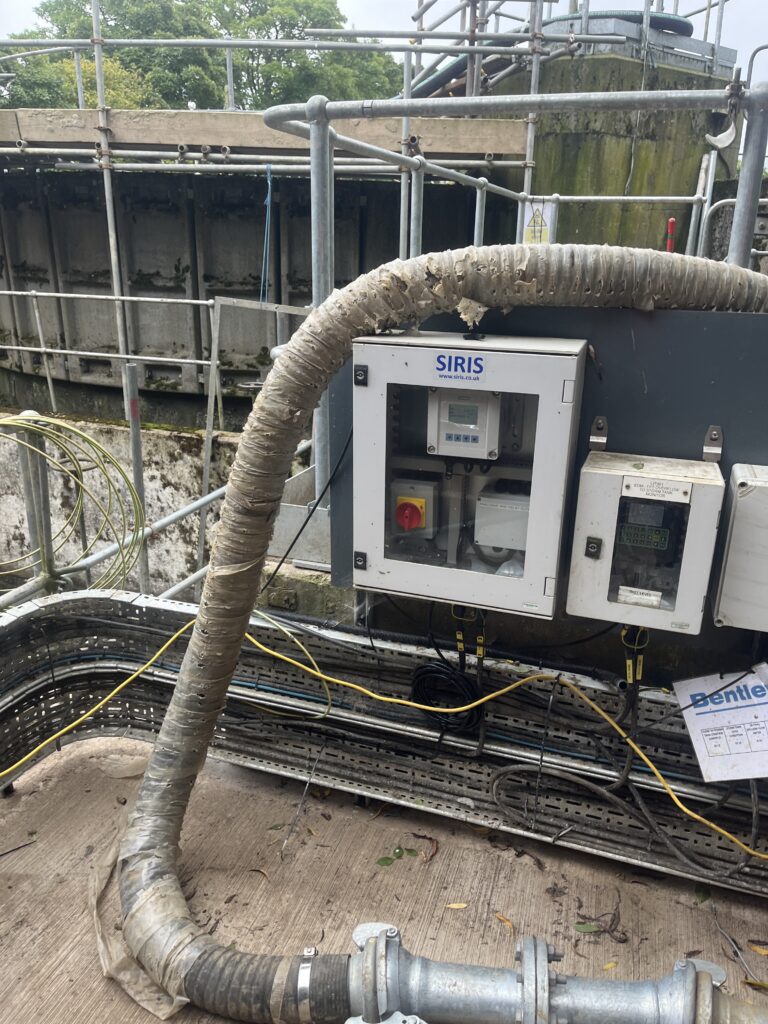
Learn about our Open Channel Ultrasonic Flow Meter range
We have a flow system solution for every need