Clamp On Ultrasonic Flow Meters
An Introduction
Clamp on ultrasonic flow meters are a type of flow meter used in various industrial applications, including effluent flow monitoring. Read our guide to understand their uses, working methodology, benefits and limitations.
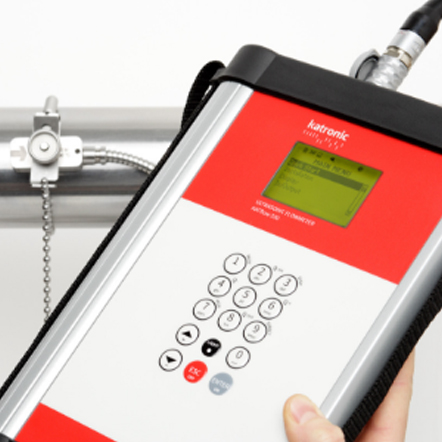
Alternative terminology for clamp on ultrasonic flow meters
Clamp-on ultrasonic flow meters are also known by several alternative names, depending on the manufacturer, industry, or specific features of the device. Some of the alternative names you may hear include:
- Non-invasive ultrasonic flow meter
- External ultrasonic flow meter
- Clamp-on transit-time flow meter (Specifically referencing the transit-time method used by some clamp-on ultrasonic flow meters)
- Clamp-on Doppler flow meter (Specifically referencing the transit-time method used by some clamp-on ultrasonic flow meters)
- Strap-on ultrasonic flow meter Some manufacturers use “strap-on” instead of “clamp-on” to describe the installation method, emphasizing that the transducers are strapped or clamped onto the pipe.
- Portable ultrasonic flow meter Some clamp-on ultrasonic flow meters are designed to be portable, allowing them to be easily moved and installed on different pipes for temporary flow measurement applications.
- Wireless ultrasonic flow meter Some models of clamp-on ultrasonic flow meters offer wireless communication capabilities for data transmission, enabling remote monitoring and control.
- Non-contact flow meter Due to being installed on external pipework
These alternative names may be used interchangeably depending on the context or preferences of users and manufacturers.
Applications of clamp on ultrasonic flow meters
Clamp-on ultrasonic flow meters are used across multiple industries where non-intrusive flow measurement is required. Some common applications include:
- Water and wastewater management: The meters can be used to measure flow without cutting into the pipe, making them a useful option particularly in temporary flow monitoring scenarios.
- Oil and gas industry: Clamp-on ultrasonic flow meters are employed for measuring the flow of crude oil, refined petroleum products, natural gas, and various chemicals in pipelines. They can be useful in applications where the fluid being measured is corrosive, volatile, or under particularly high pressure.
- HVAC (Heating, Ventilation, and Air Conditioning) systems: Clamp on flow meters can be used for monitoring the flow of water or other fluids in heating and cooling systems of buildings, including commercial and residential complexes, supporting in energy efficiency and temperature control measures.
- Chemical processing: Clamp-on ultrasonic flow meters can be utilised to monitor and control flow rates in industries such as pharmaceuticals, food and beverage, and chemical production
- Power generation: Clamp-on ultrasonic flow meters can be used to measure the flow of water, steam, or other fluids in piping systems critical to power generation processes.
- Mining and mineral processing: In mining operations, these flow meters can be used to monitor the flow of various liquids such as water, acids or slurries.
- Pulp and paper manufacturing: Clamp-on ultrasonic flow meters can be utilised to monitor chemicals and pulp slurries during various stages of paper production.
- Agricultural irrigation: These flow meters are employed in agricultural irrigation systems to measure the flow of water in pipes, helping farmers optimise water usage and improve crop yield while conserving resources.
- Pharmaceutical and biotechnology: In industries requiring stringent sanitary conditions, such as pharmaceutical and biotechnology manufacturing, clamp-on ultrasonic flow meters can be used to measure the flow of liquids without the risk of contamination.
- Building management systems: In large buildings and complexes, these flow meters can be integrated into building management systems to monitor and regulate water flow for domestic use, firefighting systems and other utilities.
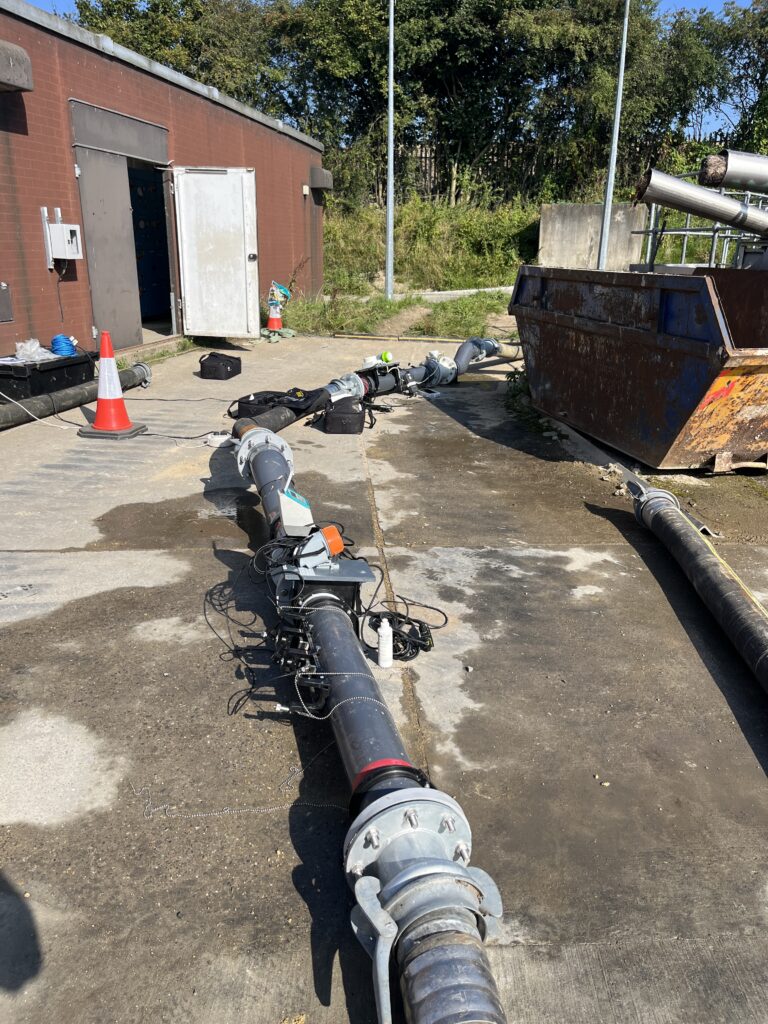
ADVANTAGES
Advantages of clamp on ultrasonic flow meters
Clamp on ultrasonic flow meters offer several benefits within effluent flow monitoring applications:
- Non-intrusive installation One of the primary advantages of clamp on ultrasonic flow meters is their non-intrusive installation method. They are simply clamped onto the outside of existing pipes, eliminating the need for cutting into the pipe or interrupting the flow of effluent. This means minimal downtime during installation and no risk of contamination from the process.
- Minimal maintenance Since clamp-on ultrasonic flow meters do not come into contact with the fluid being measured, they have minimal maintenance requirements. There are no moving parts within the flow path to wear out or clog, reducing the need for regular maintenance and ensuring long-term reliability.
- Wide range of pipe sizes Clamp on ultrasonic flow meters are available in numerous sizes and can be used with a wide range of pipe sizes and materials
- Versatility These flow meters can measure effluent flows containing various types of solids, gases, and liquids, making them suitable for diverse industrial applications. They can handle corrosive, abrasive, or high-temperature effluent streams.
- Remote monitoring and data logging Many clamp on ultrasonic flow meters come equipped with features for remote monitoring and data logging. This allows operators to track effluent flow rates in real-time and access historical data for analysis, optimisation, and compliance reporting purposes.
- Cost effectiveness Clamp-on ultrasonic flow meters require less infrastructure modification during installation and have lower ongoing maintenance costs.
DISADVANTAGES
Disadvantages of Clamp On Ultrasonic Flow Meters
There are however key disadvantages/limitations to consider in the use of clamp on ultrasonic flow meters for effluent flow monitoring:
- Limited accuracy in non-ideal conditions Clamp on ultrasonic flow meters may struggle to maintain accuracy in certain conditions, such as highly turbulent flow, entrained air or gas bubbles in the effluent, or situations where the pipe is not completely filled. These factors can affect the transmission of ultrasonic signals and compromise measurement accuracy.
- Dependence on pipe material and condition The accuracy of clamp on ultrasonic flow meters can be influenced by the material and condition of the pipe. Irregularities in pipe walls, rough surfaces, or the presence of coatings or liners may affect the transmission of ultrasonic signals, leading to inaccuracies in flow measurements.
- Limited compatibility with pipe material While clamp on ultrasonic flow meters are compatible with a wide range of pipe materials, certain materials may pose challenges. For example, very thick-walled or heavily-insulated pipes may weaken ultrasonic signals, affecting measurement accuracy.
- Sensitivity to mounting conditions Proper mounting of the transducers is crucial for accurate flow measurement. Incorrect positioning or inadequate coupling between the transducers and the pipe surface can lead to signal loss or distortion, resulting in measurement errors.
- Flow profile requirements Clamp on ultrasonic flow meters typically require a fully developed flow profile to ensure accurate measurements. In applications where the flow profile is not well-established, such as near pipe bends, elbows, or obstructions, the accuracy of the flow meter may be compromised.
- Limited temperature and pressure range While many clamp on ultrasonic flow meters can operate within a wide range of temperatures and pressures, there may be limitations in extreme conditions.
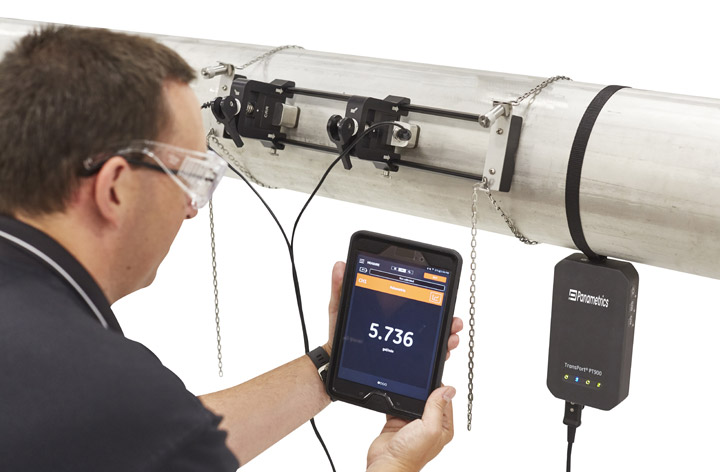
How are clamp on ultrasonic flow meters installed?
- Surface Preparation The pipe is cleaned and any debris, coatings, or contaminants from the surface of the pipe removed. Ideally, there should be a straight section of pipe with sufficient length for proper ultrasonic signal transmission and where the pipe diameter is consistent.
- Transducer Placement The transducers of the clamp-on ultrasonic flow meter are clamped onto the outside of the pipe carrying the effluent. The placement is critical for ensuring accurate measurements, typically requiring a straight section of pipe with sufficient acoustic coupling between the transducers and the pipe surface. Ultrasonic couplant gel is used to ensure no air gaps between the clamp and the pipe to enhance the sound transmission from the transducer. The transducers should be positioned opposite each other, typically at an angle of 45 to 90 degrees relative to the direction of flow.
- Configuration and calibration Once the transducers are securely attached, the flow meter settings should be configured according to the specific installation and application requirements and any calibration procedures should take place in line with manufacturer’s guidelines.
- Ultrasonic signal transmission The flow meter emits ultrasonic signals from one transducer through the pipe wall and into the effluent. The signals travel through the effluent, experiencing changes in frequency and velocity depending on the flow characteristics.
- Signal reception and analysis The second transducer receives the ultrasonic signals after they have travelled through the effluent. The flow meter analyses the received signals to determine characteristics such as flow velocity, direction and flow profile.
- Measurement method Depending on the flow conditions and the design of the flow meter, it may utilise either the Doppler effect or the transit time method for flow measurement.
- Doppler effect In conditions with solids/bubbles within the water, the flow meter may use the Doppler effect to measure flow velocity, where an ultrasonic beam is reflected off small particles or air bubbles/turbulence within the liquid. Changes in frequency between transmitted and received signals indicate the velocity of the effluent.
- Transit time method: By comparing the transit times of ultrasonic pulses both in the direction of flow and opposite to the flow direction, the flow meter can calculate flow velocity.
- Calculating flow rate Once the flow velocity is determined, the flow meter calculates the volumetric flow rate by multiplying the velocity by the cross-sectional area of the pipe.
- Environmental considerations Effluent flow monitoring may involve dealing with fluids that contain solids, gases, or varying chemical compositions. The flow meter must be capable of handling these factors without compromising accuracy or performance. This is sometimes a limiting factor when choosing a clamp on ultrasonic flow meter
- Data processing and reporting The flow meter’s electronics process the measured data and may provide real-time flow rate readings on a display or transmit the data to a central monitoring system for further analysis, logging, and reporting.
Clamp On Ultrasonic Flow Meters from SIRIS
A Convenient Alternative to Electromagnetic Options
At SIRIS, we use clamp on meters primarily for the verification of electromagnetic flow meters, however they can also provide a convenient alternative to applications where the cost or installation of an alternative flow monitoring system is prohibitive.
These units are also available for hire and can provide a temporary flow measurement solution.